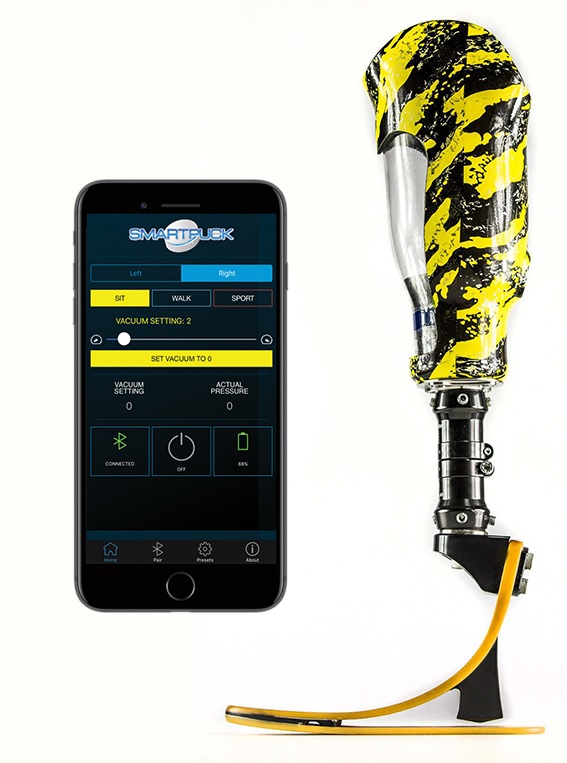
Not long ago, our friends at Bionics for Everyone shared a brief item about a British startup called Unhindr that’s developing a smart socket. The company doesn’t use the term “smart socket,” but that’s unquestionably what they’re making—a device with enough brains to adjust its grip on your residual limb in response to changes in pressure, temperature, volume, and so forth. Since phones, cameras, toasters, showerheads, and just about every other appliance has got intelligence these days, we thought intelligent sockets were long overdue.
As it turns out, smart sockets have been in the pipeline for a while. The earliest iteration we could find, the SmartPuck, dates to 2014. Developed by Colorado prosthetists Royce Heck and Clint Accinni at 5280 Prosthetics, the SmartPuck enables users to adjust their socket’s vacuum seal via a smartphone app. Gyrometers and other sensors embedded within the socket constantly monitor the fit, providing real-time data to the wearer and responding to his/her commands. “It’s kind of like the Sleep Number bed,” Accini told Innovation News. “People can find the right vacuum setting and they can change it at will. . . . [W]hen we give patients control of their prosthesis, it’s a game changer. No longer is the prosthetist the only one with control over how the prosthesis fits.”
There’s now a whole family of Puck products—ZeroPuck, MagPuck, AirPuck, VaporPuck—and a fledgling body of rudrmentary research to test the SmartPuck’s benefits over standard socket technologies. Meanwhile, a range of other companies and academic investigators have entered the smart socket sweepstakes. Here’s a quick rundown of what’s already here and what might be coming.
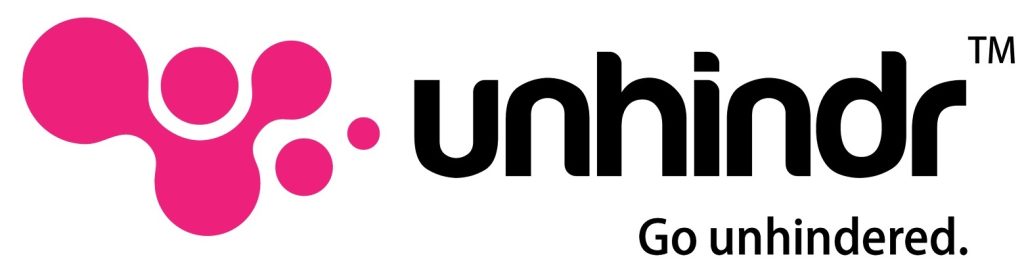
Unhindr
This is the UK-based company Bionics for Everyone spotlighted, and it’s leading the race to bring a new product to the market. Unhindr has amassed more than ₤1.2 million in seed funding, much of it earned via competitive innovator / incubator awards. Its partners and sponsors include health care heavyweights such as the National Health Service, Imperial College London, the MedTech SuperConnector, and the European Institute of Innovation and Technology.
The product itself is a robotic liner (trade named Roliner) that continuously and automatically adjusts socket pressure via built-in sensors and microfluidic technology. You can manually override the system via your smartphone to suit your personal preferences. Roliner also has an AI component, so it learns your individual tendencies and needs over time.
Unhindr had planned to start clinical trials this year, but COVID delays have pushed that date back to early 2022. Here’s a quick video introduction to the company and the product.
Korean Institute of Machinery and Materials
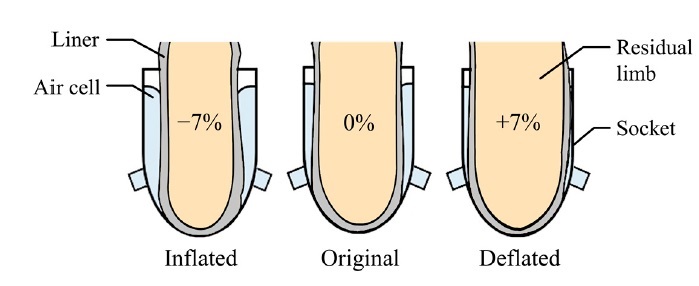
Earlier this year, a quartet of Korean researchers unveiled a socket system that operates on a system similar to the Roliner. “The proposed socket uses an inflatable air bladder to monitor the pressure in the socket and keep the pressure distribution uniform and constant while walking,” wrote the authors, who are affiliated with the Korea Institute of Machinery and Materials and the Kyungpook National University College of Engineering. The device relies on a closed-loop algorithm, rather than AI, to communicate feedback from the limb to the socket.
This device has some data behind it, in the form of trials conducted on a gait simulator. The authors tested weight loads equivalent to those exerted by individuals of 110, 155, and 200 pounds, with residual-limb volume changes of up to 7 percent (plus or minus). Throughout these experiments, the socket successfully adjusted to changes in the simulated limb. “Even if the volume of the residual limb was changed,” they wrote, “the pressure in the prosthetic socket remained the same.”
We couldn’t find any info about when (or whether) this concept will get translated into a prototype and tested on actual amputees. As soon as we hear anything, we’ll pass it along.
University of Washington
In a paper published earlier this year by the Institute of Electrical and Electronics Engineers, a team of UW bioengineers described a motor-driven, auto-adjusting socket for below-knee amputees. This system uses a thin antenna to constantly monitor the residual limb’s position relative to the socket wall, with adjustable panels that flex to maintain uniform distance between limb and socket.
A prototype of this system achieved impressive results in laboratory tests. The smart socket maintained a constant fit on 10 below-knee amputees walking on treadmills, with average variations of just .003 of a millimeter. “The capability of the control system to maintain and respond to a change in set point indicates that it is ready for evaluation outside of the laboratory,” the authors conclude. We’ll give you updates on those tests ASAP.
Virginia Tech College of Engineering
A multidisciplinary engineering team at the Virginia Tech College of Engineering is midway through a three-year, $400,000 project to develop a smart prosthetic socket. The team includes an undergraduate engineering student who is an above-knee amputee. They’re also working in consultation with Ability Prosthetics and Orthotics of Charlotte, NC, and a biomechanics group on campus that studies gait, balance, and fall prevention.
To establish baseline data about the nature and extent of residual limb changes during normal daily activities, the researchers are using digital imaging technology and high-precision laser scanning. The smart socket itself will be equipped with fluidic flexible matrix composites, a responsive material that can achieve minute variations in shape, pressure, and stiffness.
The concept has been prototyped in the lab. Stay tuned for info on preliminary data and/or trials.