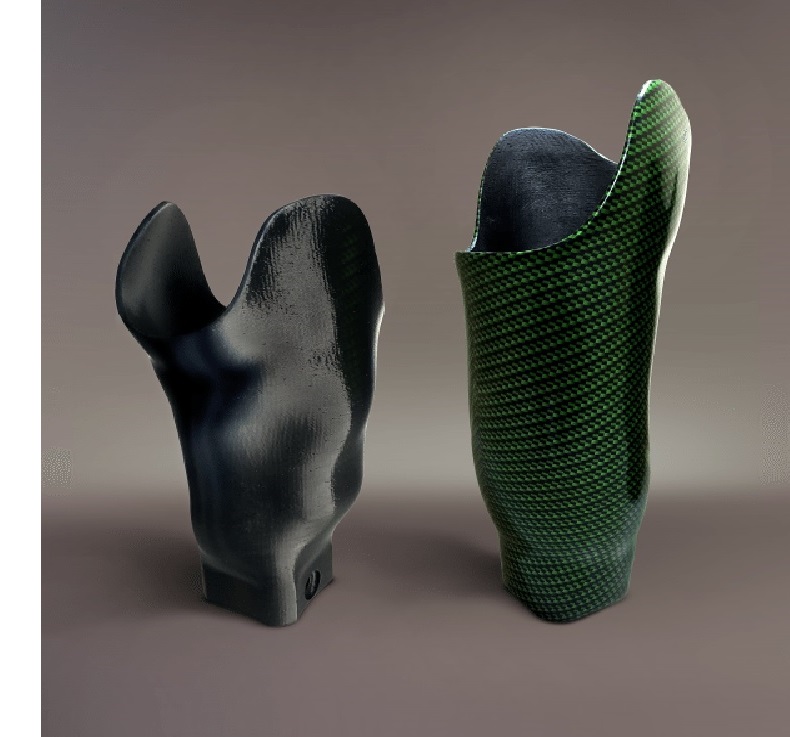
Advancements in 3D printing allow prosthetists to custom-design lightweight, affordable, highly functional limbs for their patients. But conventional 3D-printing materials tend to rub residual limbs the wrong way, which makes it difficult to achieve a truly comfortable fit.
Two industry players have teamed up to tackle that problem with a new line of biocompatible 3D-printing materials. The collaboration unites Essentium, a worldwide leader in industrial additive manufacturing (AM), and Vorum, a world leader in O&P design software. market. The new materials are billed as non-contact sensitive, non-cytotoxic, and non-irritant, giving prosthetists a new option that’s suitable for devices that require extensive skin contact.
“Modern O&P devices are often designed with a more intimate fit than in the past, which means we need to consider how the patient’s skin might behave in direct contact with the final prosthesis,” says Vorum CEO Angela Saunders. “It’s imperative to have certified materials so that the 3D-printed devices work with the body, not against it.”
“Developing comfortable, properly fitting orthotics and prosthetics is not just a science but also an art,” adds Essentium CEO Blake Teipel. “Our biocompatible materials, combined with advanced 3D-printing platforms, means clinicians can use their skills to create devices better, faster, and cheaper than before—which also means O&P devices that are more accessible, comfortable, and affordable for many more people around the world.”
Vorum has 30 years of experience in digital processes for the prosthetics industry, offering clinicians a proven approach for 3D-printing adoption, implementation, training, and support. The partnership with Essentium gives prosthetists the ability to swiftly transition from plaster-casting methods to 3D-printing.
The new materials meet ISO 10993 and US FDA guidance for intact skin surface devices as verified by certified, independent lab testing.